PRI-SC®
Hydrogen Peroxide Regenerated Iron for Sulfide Odor Control
Sulfide odor control within sanitary sewers has been practiced for over 50 years, yet only recently have substantive advances been made. Where once the choice of chemical treatment was either chlorine or iron salts, safer and more environmentally benign technologies based on nitrates, hydrogen peroxide, and/or magnesium hydroxide have gained acceptance. These new alternatives, however, can increase treatment costs substantially and present limitations in themselves. Therefore, it makes sense to explore new avenues for lessening the adverse impacts of the older, cheaper mainstays, particularly iron salts (ferrous/ferric chloride or sulfate) that provide other benefits to wastewater treatment operations.
USP Technologies has addressed this need through development of its proprietary technology called PRI-SC® (Peroxide Regenerated Iron-Sulfide Control®). PRI-SC® is a combination treatment that integrates iron salts with hydrogen peroxide (H2O2) in a synergistic fashion. At the most basic level, PRI-SC® treatment may be viewed as an oxidant (hydrogen peroxide) regenerating the spent iron salt (FeS) in-situ, yielding fresh ferrous (Fe+2) or ferric (Fe3+) iron and colloidal sulfur.
The combined treatment provides cost benefits superior to either chemical alone, while allowing greater flexibility as to the placement of storage and dosing facilities. For example, practical control of sulfides to very low levels (e.g. < 0.1 mg/L dissolved sulfide) is afforded with minimal reaction time (< 5 minutes). Other benefits are accrued to the reaction, including: reduced solids (FeS) loadings, accelerated reaction rates and enhanced flocculation (in clarifiers).
The conceptual basis of PRI-SC® is to use the iron for primary sulfide control, and use the H2O2 to regenerate the iron from FeS. The process can be represented as a regenerative cycle (below), where a working inventory of iron is maintained with H2S as the input, elemental sulfur as the output, and H2O2 as the driver. The regenerated iron species (ferrous or ferric) is determined by the amount of H2O2 that is added to drive the oxidation step of FeS. The form of iron that is generated can then be directed toward various subsequent applications.
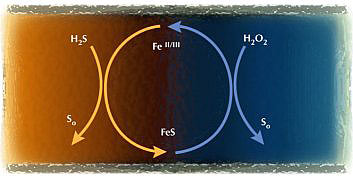
PRI-SC® in Practice
In practice, PRI-SC® involves adding an iron salt at the upper reaches of the collection system and using hydrogen peroxide to regenerate the "spent" iron (FeS) at one or more points downstream. The analogy is one of a capturing agent (iron salt) added at the top of an interceptor, which then absorbs dissolved sulfide as it moves down the line. Intermittent hydrogen peroxide injection serves to regenerate the capturing agent thereby allowing additional sulfide to be absorbed downstream.
Incorporating a final regeneration site at the treatment plant provides rapid oxidation of sulfides to very low levels, effectively reducing the H2S loading to the influent scrubbers, and hydrous ferric iron that can be used for additional odor control in primary treatment or for enhanced clarification. The process has particular benefit when employed for gravity interceptors, force main discharges and headworks treatment.
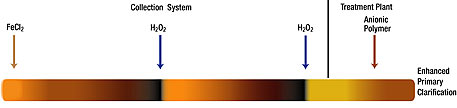
Example 1. Collection system sulfide control (PRI-SC®)
When applied to collection systems, the conceptual basis of PRI-TECHTM is to use iron for primary sulfide control, and use the H2O2 to regenerate the iron from FeS. This is similar to what happens naturally in gravity interceptors where re-aeration regenerates the spent iron salt, but PRI-SC® accomplishes this in a more harnessed fashion. The process can be represented as a regenerative cycle, where a working inventory of iron is maintained with H2S as the input, elemental sulfur as the output, and H2O2 as the driver for the oxidative regeneration step.
The basic process occurs in three steps:
- 1) Iron complexation with dissolved sulfide;
- 2) H2O2 oxidation of the FeS complex to provide elemental sulfur and free iron (free ferrous or hydrous ferric iron); and
- 3) Complexation of additional sulfide by the ferrous iron.
The inherent cost benefit of PRI-TECHTM compared to traditional iron salt use is derived from the relative cost of the two chemicals and the stoichiometric relationship in the above net reactions. As an example, the net reaction for the basic ferrous regeneration (sulfide oxidation) shown below requires 0.83 lbs of Fe (1.87 lbs of FeCl2) and 0.5 lbs of H2O2 per pound of sulfide and in essence only 0.6 lbs of H2O2 are required to generate 1 lb of Fe+2. Based on the typical relative cost of the two chemicals this yields a savings benefit of 30% to 50% compared to straight iron salts.
Step 1: H2S + FeCl2 → FeS + 2HCl
Step 2: FeS + H2O2 → S0 + Fe(OH)2
Step 3: Fe(OH)2 + H2S → FeS + 2H2O
Net: 2H2S + FeCl2 + H2O2 → S0 + FeS + 2HCl + 2H2O
Back to top
Get More Information
Contact USP Technologies for more information on our products and services: