Case Study for Control of H2S in Municipal Sludge Using Hydrogen Peroxide
In many municipal treatment facilities, the processing of wastewater sludge (biosolids) poses operational and safety challenges due to hydrogen sulfide (H2S) generation. In addition to being a hazard to operations personnel (H2S is a poisonous gas), H2S odors generated during sludge processing can cause community complaints and make plant working conditions unpleasant. Furthermore, damage to equipment and concrete structures caused by H2S initiated corrosion can be substantial. Typical areas where H2S problems occur include gravity thickeners, mix tanks, and dewatering presses.
Hydrogen sulfide is generated in sludge via the same mechanism as in collection systems - conversion of sulfates to sulfides by bacteria. This biochemical generation of hydrogen sulfide is brought about by anaerobic or oxygen limited conditions. There are numerous chemical and non-chemical treatment technologies available which can control H2S in municipal sludge processing operations. This article will discuss the use of hydrogen peroxide for sludge treatment and give real world examples from field experiments and full scale plant use.
In municipal wastewater, the reaction time required for complete oxidation of hydrogen sulfide by hydrogen peroxide typically ranges from 10-30 minutes depending on temperature, pH, and dissolved metal concentrations. In municipal sludge the reaction rate is much faster. Usually, 5 minutes or less are required for complete removal of hydrogen sulfide. The faster reaction rate in sludge is due to relatively high concentrations of solids, metals, and other catalytic materials. This rapid oxidation of H2S permits hydrogen peroxide to be added only a few minutes ahead of the sludge presses and react completely without interfering with dewatering polymers. In sludges a H2O2 to sulfide (liquid) ratio between 5:1 and 10:1 is usually required for complete oxidation.
Although the hydrogen peroxide reacts quickly with hydrogen sulfide in sludge, its effect on H2S is not short lived. One of the reaction products of hydrogen peroxide decomposition is oxygen (O2). The additional O2 provided by hydrogen peroxide will help maintain aerobic conditions in the sludge, and suppress hydrogen sulfide regeneration for hours. This extended effect allows H2O2 to be added further upstream to destroy H2S (e.g., in sludge mix tanks), and still maintain H2S control at the dewatering presses.
Other Oxidants such as potassium permanganate (KMnO4) are also used for hydrogen sulfide control in municipal sludge. Potassium permanganate must be added immediately before dewatering because it reacts instantaneously with H2S, and does not effectively suppress H2S regeneration. Therefore, it cannot be added to mix tanks or thickeners and maintain hydrogen sulfide control in subsequent stages of the sludge processing operation.
An example of hydrogen peroxide's ability to suppress hydrogen sulfide regeneration was observed while conducting experiments at a municipal treatment facility in the Northeast. Facility personnel wished to oxidize H2S in their sludge mix tanks to reduce potential exposure to operators, and to reduce odors and equipment corrosion. Furthermore, it was hoped that chemical treatment in the mix tanks would maintain control of hydrogen sulfide until the sludge reached the belt filter presses. The residence time in the mix tanks ranged from 1-2 hours depending on flow rates of primary and secondary sludge. From the mix tanks, sludge is pumped directly to several large belt filter presses. Experiments compared H2O2 to potassium permanganate (KMnO4) to determine the most effective method to control H2S at both the mix tanks and the filter presses using a single chemical addition point.
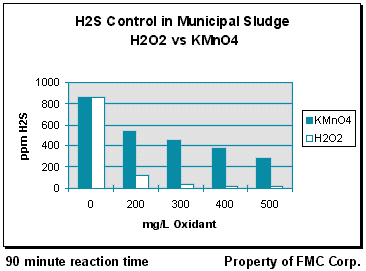
Data was collected at average sludge mix tank holding times (~90 minutes). Baseline H2S (air) measurements taken from about 6 inches above the surface of the sludge showed hydrogen sulfide concentrations exceeding 850 ppm. Subsequent to these initial measurements, H2O2 or KMnO4 was metered into the sludge at concentrations ranging from 200-500 mg/L (100% oxidant basis). After addition of the prescribed concentration of oxidant (with mixing) the sludge was held for 90 minutes without further chemical treatment. After 90 minutes, Measurements of H2S (air) were again taken from just above the surface of the sludge. Results showed that H2O2 treatment reduced H2S levels by 87-99% across the range of dose rates. The KMnO4 treatments were not as effective, with hydrogen sulfide reductions of 38-68% over the same range of oxidant concentrations. These results are shown graphically here.
This study demonstrated that hydrogen peroxide can control H2S for extended time periods. In addition, H2O2 was clearly superior to KMnO4 when comparable concentrations of each oxidant were used. This information, combined with the lower cost of H2O2 ($0.685/lb H2O2 100% basis vs. $1.21/lb KMnO4 100% basis) made hydrogen peroxide a more cost effective choice for this municipality.
The City Of Orlando, FL
The City of Orlando processes sludge at their WATER-CONSERVE 1 Plant. Sludge is pumped to 2 belt filter presses from digesters located adjacent to the sludge processing building. Typical sludge feed rates to each of the presses ranges from about 85-100 GPM (170-200 GPM total). In order to control odors and protect operations personnel from hydrogen sulfide exposure, hydrogen peroxide is injected into the sludge lines feeding the presses. The reaction time in the line prior to reaching the belt filter press is only about 3-5 minutes.
Recently, air and filtrate sampling was conducted during sludge processing to examine the level of hydrogen sulfide reduction achieved with H2O2 treatment. With a sludge feed rate of 175 GPM and the H2O2 off, H2S levels above the presses ranged from 18-42 ppm in the air. Filtrate samples collected during this time showed a hydrogen sulfide concentration of 5 mg/L in the liquid. When H2O2 treatment was initiated at a concentration of about 35 ppm (0.6 GPH 50% H2O2) the H2S levels in the air above the presses were quickly reduced to non-detectable levels (STX70 model H2S monitor - Industrial Scientific Inc.). Sulfide levels in the filtrate were likewise reduced to non-detectable levels. These reductions in hydrogen sulfide levels were observed within 5 minutes of starting H2O2 treatment, allowing quick response to unexpected increases in H2S concentrations in the sludge.
The hydrogen peroxide used for this application is stored in a USP Technologies designed hydrogen peroxide dosing system which contains the double-contained polyethylene storage tank, pumps, control panel and ChemWatch remote tank monitoring system (see Services Offered by USP Technologies or ChemWatch Monitoring Program information).
Summary
The unique chemistry of hydrogen peroxide makes it a versatile tool for destruction of H2S in sludge processing operations. It can be added to sludge lines just prior to dewatering presses to quickly eliminate H2S, or used in mix tanks and thickeners to control H2S generation for longer periods of time. The following advantages of hydrogen peroxide should be considered when evaluating sludge treatment options:
- Rapid, complete oxidation of hydrogen sulfide
- Hydrogen peroxide decomposition liberates oxygen which helps maintain aerobic conditions, inhibiting H2S regeneration.
- No capital expenditures for storage and handling equipment when using USP Technologies' H2O2 dosing systems.
- The safe and effective use of hydrogen peroxide is backed up by USP Technologies - with over 20 years experience in environmental applications for hydrogen peroxide.
Back to top
Get More Information
Contact USP Technologies for more information on our products and services: