Hydrogen Sulfide Control - Headworks Odor Control with Hydrogen Peroxide
Michael Fagan and John R. Walton, USP Technologies (formerly US Peroxide)
March 17, 1999
For over 50 years the standard way to deal with odors entering wastewater treatment plants was to pre-chlorinate the influent sewers.1 Recently, however, an increasing number of POTW's have revisited this issue and come up with a different answer - hydrogen peroxide (H2O2). Their results show that H2O2 can replace chlorine with little to no increase in costs, and with notable benefits to downstream operations. This paper looks at four recent studies conducted at large municipalities and identifies the factors that led them to select H2O2 for liquid-phase headworks odor control.
Reasons for Increasing Use of Hydrogen Peroxide
Industry trend to eliminate chlorine (and its associated risks).
OSHA's Process Safety Management (PSM) standard - 29 CFR 1910.119 - was passed into law in 1992 and came into enforcement in May 1997. The PSM standard requires that facilities undergo comprehensive preparedness for catastrophic releases of certain toxic materials. This involves process hazards analysis, standard operating procedures, employee training, incident investigations, emergency planning and response, and periodic compliance audits. As a toxic compressed gas, chlorine is subject to these regulations if stored in quantities > 1500 lbs. This includes the standard industry packaging unit - one-ton cylinders. The costs to comply with the law have been estimated as follows.
Facility modifications | $1,000,000 - 3,000,000 |
Initial documentation and set-up | $ 150,000 - 500,000 |
Total | $1,150,000 - 3,500,000 |
NB. Facility modifications include negative pressure storage rooms equipped with emergency vapor treatment systems (complete with back-up power, etc.) to contain and neutralize an accidental release.
In addition, the law states that PSM programs must be maintained and audited no less than every three years. This can add another $25,000 - 75,000 per year to the cost. Plus, there are costs for supplemental liability insurance. Clearly, these issues impact on the actual cost for using chlorine. For a typical facility using 2-3 tons a day, the full cost for chlorine can increase from about $150 to $250-400 per ton. Significantly, the standard industrial strengths of H2O2 (35% and 50%) are exempt from the PSM ruling.
Lower cost of H2O2 compared to other chemicals.
A logical first response to the increasing costs for chlorine is to change to liquid chlorine (sodium hypochlorite, NaOCl), which is not a PSM-listed material. However, NaOCl costs about five times chlorine on an active basis. This then opens the field to other non-chlorine odor control agents, such as H2O2. As it turns out (for headworks odor control), H2O2 is considerably cheaper than NaOCl, with the actual costs being closer to chlorine (see Figure 1).
The two cost factors for H2O2 are the dose ratio and unit price. Dose ratios are covered in the case studies that follow. The unit price for H2O2 has dropped consistently over the past 20 years as production has increased ten-fold to satisfy the exploding demand for chlorine-free products, especially in the pulp and paper industry. When adjusted for inflation, H2O2 today costs 70-80% less than it did in the early 1980's.
Figure 1. Comparative costs for headworks odor control chemicals -
(typical costs to treat 200 lbs/day of liquid-phase H2S, e.g., 5 mg/L in 5 mgd).
Oxidizer | Practical Weight Ratio (as 100%) | Typical Unit Cost | Requirement (per day) | Effective Cost ($ per day) |
Chlorine (bulk) | 6-8:1 | $150/Ton | 0.6-0.8 Tons | $90-120 |
Chlorine (cylinders) | 6-8:1 | $250/Ton | 0.6-0.8 Tons | $150-180 |
Sodium Hypochlorite (12.5 %, 1.1 lbs/gal) | 6-8:1 | $0.40/Gal | 960-1280 Gals | $380-510 |
Hydrogen Peroxide (50 %, 5.0 lbs/gal) | 1.2-1.5:1 | $3.45/Gal | 48-60 Gals | $165-210 |
Efficient reaction of H2O2 with H2S.
At the pH of municipal wastewaters, the reaction of H2O2 with sulfide is as follows, yielding elemental sulfur and water.
H2O2 + H2S ----> S + 2H2O |
Molecular weight......... | 34 | 34 |
Weight ratio ........ | 1.0 | 1.0 |
The efficiency at which this occurs in practice depends on many factors, the most important of which are available reaction time and duration of control. The optimal range is typically between 5-20 minutes and 1-2 hours. Operating outside of this range is most likely the reason why values reported in much of the literature are 4-8 times the theoretical requirement. However, as the case studies in this paper show (see Figure 2), practical ratios much closer to theoretical are attainable if one can operate nearer to the optimal range.
Figure 2. Effective H2O2 : S dose ratios (per recent case studies)
| Aqueous Sulfide Level |
Municipality | Effective Dose Ratio (by weight) | Available Reaction Time (mins) | Before (mg/L) | After (mg/L) | Difference % |
San Jose, CA | 1.4 | 5 - 10 | 2 - 4 | 0.3 - 0.5 | 80 - 90 |
MWRA (Boston, MA) | 1.3 | 8 - 10 | 3 - 5 | 0.2 - 0.3 | 90 - 95 |
Hyperion (Los Angeles) | 1.2 | 8 - 10 | 3 - 5 | 0.3 - 0.5 | 90 - 95 |
So what becomes of the excess H2O2? Does it react with ammonia or the many organics present in the wastewater, as do chlorine and hypochlorite? No - it decomposes to oxygen and water. This can be confirmed by tracking dissolved oxygen which typically show a stoichiometric increase in relation to excess H2O2 - 1 mg/L residual H2O2 will release 0.5 mg/L D.O. For headworks applications, this results in a profile typified in Figure 3 (below). This has practical value in controlling sulfide generation in downstream clarifiers - an aspect not afforded by chlorine or hypochlorite.
Figure 3. Typical H2O2 - Sulfide reaction profile (in domestic wastewater).
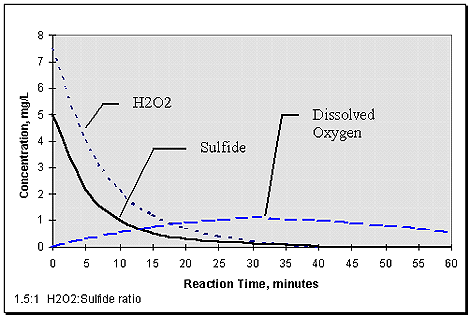
Case Studies
San Jose / Santa Clara Water Pollution Control Plant (San Jose, California)
The San Jose / Santa Clara WPCP contracted with U.S. Peroxide, LLC in 1996 to conduct a three-month demonstration of H2O2 in an effort to improve control of odors emanating from its headworks and primary clarifiers. Expanding the existing chlorine facilities to meet these goals would have involved major upgrades required by the newer fire codes and Process Safety Management regulations. Details of this study are contained in the project report which is summarized below.3
Background
The San Jose / Santa Clara WPCP is a 130 MGD tertiary treatment facility that receives sewage from three interceptors (see Figure 6). During peak PM flows, a portion of the primary effluent is diverted to a 20 MGD equalization basin, and fed to the secondary units during the low flow early AM. Chlorine is injected at two locations for odor control from April to October: at the influent to the headworks (10,000-15,000 lbs/day); and at the influent to the equalization basin (3,000-5,000 lbs/day). This corresponded to a dose ratio at the headworks of 7-8:1 (w/w chlorine:sulfide). The primary reasons for considering H2O2 in lieu of other chemical alternatives were the success of other municipalities in converting from chlorine to H2O2, and the favorable price trend for H2O2.
Figure 6. San Jose / Santa Clara WPCP Influent Flows.
Trunkline | Flow (mgd) | Available Reaction Time | Typical Total Sulfide (mg/L) |
San Jose | 75 | 3 mins | 1.8 |
Milpitas | 10 | 5 mins | 2.4 |
Santa Clara | 40 | 6 mins | 2.0 |
Findings
The initial baseline survey indicated that about 2000 lbs/day (or 1.8 mg/L) of sulfide was entering the treatment plant from the collection system. Another 825 lbs/day (or 0.7 mg/L) was being generated within the primary clarifiers. This explained why chlorine injection at the headworks was not controlling odors off the clarifiers. The approach taken with H2O2 was thus two-fold: 1)utilize a single injection point into each of the interceptors discharging into the headworks; and 2) provide a booster dose into the influent to the primary clarifiers.
The results showed that a H2O2:S dose ratio of 1.4:1 achieved the target level of control at the headworks (< 0.5 mg/L). For the clarifiers, the combination of headworks injection (2.5 mg/L) and primary booster dose (1.5 mg/L) was shown to be most efficient, improving the cost-performance by 20% over headworks dosing alone. A significant factor in the performance of H2O2 at this facility was the use of FeCl3 in the upstream collection system (for odor control). As indicated in Figure 7 (below), the effect of 1-2 mg/L iron in the influent wastewater was to catalyze the H2O2 - Sulfide reaction, accelerating the removal of sulfide by a factor of 2-3. The conclusion was that H2O2 provided better control of H2S through the primary clarifiers than did chlorine - no treatment of the equalization basin was needed when H2O2 was added. Further, on an equal performance basis, the effective cost for H2O2 was equal to or less than that for chlorine.
Figure 7.Effect of iron on catalyzing the reaction between H2O2 and sulfide.
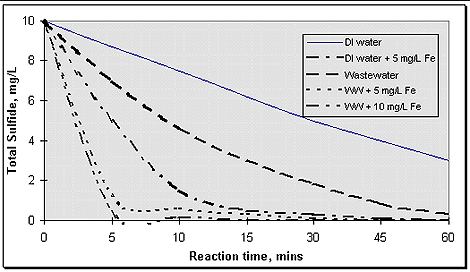
Massachusetts Water Resource Authority (MWRA - Boston, Massachusetts)
Under the direction of the Massachusetts Water Resource Authority (MWRA), Metcalf & Eddy conducted a pretreatment study in 1996 to investigate alternatives for controlling liquid-phase sulfide entering the Deer Island Treatment Plant (DITP). The results of this work were presented at the annual WEFTEC conference the following year,4 and are summarized below.
Background
The driver for the study occurred the previous summer when the headworks odor scrubbers became overloaded with > 200 ppm H2S gas, creating objectionable odors and corroding new infrastructure. Much of the sulfide is generated in the three conduits (tunnels) that transport 350 MGD of wastewater beneath the harbor to the DITP. As shown in the table below, the low velocities within these tunnels are a major factor contributing to the high sulfide levels.
Figure 8.MWRA influent flows.
Influent Tunnel | Flow (mgd) | Distance (feet) | Diameter (feet) | Retention Time (hrs) | Velocity (fps) |
Boston Main Drainage | 125 | 2000 | 10 | 3.6 | 0.15 |
Inter Island | 90 | 2650 | 11 | 5.4 | 0.14 |
North Metro Relief | 85 | 20,800 | 10 | 3.6 | 1.60 |
The study focused on one of the three lines (the Boston Main Drainage Tunnel), and looked at the four leading treatment chemicals for liquid-phase sulfide control: ferric chloride (FeCl3), sodium hypochlorite (NaOCl), hydrogen peroxide (H2O2), and calcium nitrate (Ca(NO3)2). Depending on the chemical, it was injected at either the DITP Main Pump Station (on the island, 24 minutes retention from the headworks) or the remote headworks at the front of the tunnel (on the mainland, 4 hours retention). The goal was to reduce H2S levels in the primary clarifier scrubbers to < 25 ppm (a reduction of about 90%).
Findings
Ferric chloride was tried at two injection points: first at the remote headworks; and then at the DITP Main Pump Station. When dosed at the remote headworks (at 20:1 weight ratio), process upsets occurred at the DITP in form of unsettleable solids (pin-floc), pH depression, foaming in the clarifiers and disinfection basins, and solids carryover in the gravity thickeners. Lowering the dose (to 5-10:1) eliminated these upsets but caused H2S levels to exceed the target criterion. Similar results were obtained when the FeCl3 was added at the Main Pump Station, with the additional complication of foaming and pressure build-up in an anaerobic digester. For these reasons, ferric chloride was not recommended for implementation.
Sodium hypochlorite was injected at the DITP Main Pump Station due to its fast reaction with sulfide. NaOCl achieved the target H2S removal levels, but operators found it difficult to determine the optimum dose - i.e., H2S levels did not quickly respond to dose rate changes. No operational problems resulted from the NaOCl, though the potential for chloroform formation was a concern given the plant's air quality restrictions. Also a concern was that higher doses of NaOCl could cause equipment corrosion and impact the secondary treatment process.
Calcium nitrate was added at the remote headworks since it requires mediation by the wastewater biology to control sulfide (i.e., it does not oxidize sulfide directly). When dosed at a 2.4:1 weight ratio, calcium nitrate achieved the target removal levels, but operators found it difficult to maintain the optimum doses. Careful monitoring was needed to avoid plant upsets.
Hydrogen peroxide was added at the DITP Main Pump Station due its relatively quick reaction with sulfide. When dosed at a 1.2:1 weight ratio, H2O2 lowered the H2S levels across the plant within an hour - much quicker than the other chemicals. Dosing was accurate and easy to control, with no adverse impact on operations.
Figure 9 (below) summarizes the annual operating costs estimated for the three chemicals which met the H2S removal criterion. Based on the field results, and on present and life cycle costs, M&E recommended that H2O2 be used for H2S control at the DITP.
Figure 9. Comparative dose ratios and operating costs (for H2O2, nitrate, and NaOCl)
| Average Dose Rate | |
Control Chemical | (gpm) | (mg/L) | Estimated Operating Costs |
Sodium hypochlorite - 12.5% | 6.9 | 3.7 | $434,000/year |
Hydrogen peroxide - 50% | 1.3 | 3.2 | $320,000/year |
Calcium nitrate - 54% | 3.5 | 10.4 | $1,258,500/year |
Hyperion Treatment Plant (Los Angeles, California)
The Hyperion Treatment Plant (HTP) contracted with U.S. Peroxide, LLC in 1995 to conduct a series of demonstrations using H2O2 for headworks odor control. The goal was to reduce sulfide loadings to the odor scrubbers and to improve general ambient odors around the facility. The results from this work are contained in the project report, and are summarized below.5
Background
The Hyperion Treatment Plant is a 360 MGD secondary treatment facility which uses enhanced primary clarification (FeCl3 and anionic polymer) to maximize BOD removal through the front of the plant. The baseline studies showed that the two primary contributors to headworks sulfide were the NORS and NCOS interceptors, each representing about 45% of the loading (and flow) into the plant. Total sulfide levels during the warmer months were 2.5 - 4.5 mg/L. H2S levels into the headworks scrubbers were 125-200 ppm. The demonstration consisted of three studies conducted over a two-year period, with each lasting 1-2 weeks. The specific objectives were to establish a consistent dose-response profile and to identify ancillary economic and/or operational benefits associated with the treatment.
Figure 10. Chemical injection sequence for the HTP study.
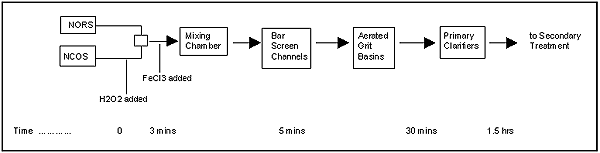
Findings
Figure 11 (below) summarizes the dose-response profile developed through the study. H2S levels into the scrubber intakes were reduced 50 - 90%, depending on the dose ratio. Ambient odors were observed to be greatly reduced, and improved oxygen transfer was noted in the secondary treatment process.
Figure 11. Dose-response profile
| Total Sulfide (mg/L) | Residual H2O2 (mg/L) |
Dose Ratio H2O2:S (w/w) | Clarifier Influent | Clarifier Effluent | Clarifier Influent | Clarifier Effluent |
Headworks | 0.6 | 0.5 | 0.9 | 0.4 |
Primary influent | 0.2 | 0.2 | 0.7 | 0.9 |
Primary effluent | 0.2 | 0.1 | ---- | ---- |
Other benefits were derived from the concurrent addition of H2O2 and FeCl3. On the one hand, the iron served to catalyze the sulfide-H2O2 reaction, increasing the rate of sulfide removal. On the other hand, the H2O2 kept the iron in an oxidized state, thereby enhancing flocculation. FeCl3 use was reduced 25-50% while H2O2 was being tested. Much of the savings can be attributed to the removal of sulfide by H2O2, which otherwise would have precipitated the iron. Further work is planned to explore this apparent synergy between concurrent H2O2 and FeCl3 addition.
Conclusions
Recent field studies prove that H2O2 is a cost-effective replacement to chlorine for controlling headworks odors. The optimized dose ratios determined in these studies are considerably less than those frequently reported in the literature. The most likely reason for this difference is that H2O2 is sometimes not used in its optimal manner (i.e., reaction times > 5-20 minutes and retention times (1-2 hours). The studies also highlight that full-scale demonstrations are needed to assess the full cost-benefit of sulfide control chemicals, especially H2O2. Apart from the obvious (i.e., reduced vapor treatment costs), the benefits of using H2O2 for headworks sulfide control include D.O. elevation and (when used in conjunction with iron) more efficient solids separation through primary clarifiers.
List of Figures
1. Comparative cost of headworks odor control chemicals 2. Effective H2O2:H2S dose ratios (per recent case studies) 3. Typical H2O2 - H2S reaction profile (in domestic wastewater) 6. San Jose / Santa Clara - Characterization of influent flows 7. Effect of iron on catalyzing the reaction between H2O2 and sulfide 8. MWRA - Characterization of influent flows 9. MWRA - Comparative dose ratios and operating costs (for H2O2, nitrate, and NaOCl) 10. Hyperion - Chemical injection sequence 11. Hyperion - Dose-response profile
References
"Project Report (San Jose / Santa Clara Water Pollution Control Plant): Odor Control at the Treatment Plant Headworks and Primary Clarifiers", U.S. Peroxide, LLC (February, 1997). McMonagle, T., S. Johnson, and R. Otoski, "Sulfide Pretreatment Program to Control Odors at the Massachusetts Water Resources Authority's (MWRA) Deer Island Treatment Plant", Paper No. 9728003, 70th Annual WEFTEC Conference (October, 1997 - Chicago, IL). "Project Report (Hyperion Treatment Plant, Los Angeles): Hydrogen Peroxide Injection into the Influent Sewers for Headworks Odor Control", U.S. Peroxide, LLC (March, 1998).
Back to top
Get More Information
Contact USP Technologies for more information on our products and services: